As an Amazon Associate, this site earns commissions from qualifying purchases. For more information click here.
Does your leaf blower run fine when cold but refuses to do so when hot? Or maybe the blower does start but suddenly halts or performs poorly. Temperature affects these tools, but with the right approach you can fix this problem and have the blower working again.
If your leaf blower refuses to start when warm, it is probably caused by old fuel in the tank. It could also be due to gas pressure buildup or a broken spark plug. Fresh fuel should be added to gas leaf blowers every 2 to 4 weeks.
Fuel Pressure Buildup
Heat causes gas to expand . If the blower fuel tank is already full, pressure will build up as the fuel occupies more space. The hotter it gets the greater the expansion of gas and the more the tank is pushed to its limits in terms of capacity. Eventually the pressure gets to the fuel line as well.
Solution. Open the gas cap and let some of the fuel evaporate. That should ease some of the pressure off. If the temperature is really high, place the blower under shade and let it cool for a few minutes. This usually solves the problem.
If the fuel tank is leaking or damaged in any way, replace with a compatible tank The Homelite Inc 308123004 Fuel Tank for example, is designed with Homelite leaf blowers only. Check your brand.
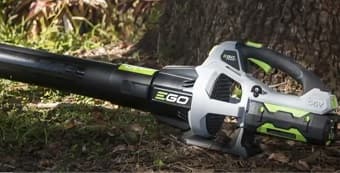
Fuel is Too Lean
A lean mix means there is more air than what is needed for combustion. Rich gas is the opposite, there is more gas than what is required for combustion. A lean fuel mix coupled with heat can give leaf blowers some difficulty in starting.
Solution. Use a bit of a richer mix, add more fuel and less air. If you are using 87 octane – the minimum requirement – replace with 93 octane or better. Some leaf blowers respond better to a richer, high octane fuel.
Wrong Fuel Mix
A 2-stroke leaf blower needs the exact ratio of gas and oil to run. Typically that is 40:1 or 3.2 ounces of oil per gallon of gas. Depending your leaf blower, the ratio might be different. If you make a mistake with the ratio, the engine will not be able to run.
Solution. Follow the manufacturer instructions on the fuel mix. Make sure there is no more than 10% ethanol. The octane has to be at least 87. If you are using a 4-stroke blower, do not mix gas and oil.
Most leaf blowers will run fine on unleaded gas. But it is best to check the manufacturer if they recommend something specific. If nothing is mentioned, unleaded gas at 87 octane is fine.
Clogged Air Filter
Blocked air filters causes two problems. First, air can no longer get into the system, which is necessary to cool the engine. Second, the lack of air and clogging leads to a temperature increase in the system. If it is already hot externally, the engine can overheat.
Solution. Clean or replace the air filter after every 50 hours of use. This is a general rule only. If you use the blower extensively, the filter might need more regular cleaning. To clean or replace the filter, follow these steps.
If you have a Husqvarna 125 125B 125BVX or 125BX, the AISEN 2-pack air filter is a good replacement.
- Turn the leaf blower off. Unplug from the power source if it is electric.
- Remove the filter cover. Refer to your manual for the location.
- You might have to remove some screws. In other models you just lift a latch.
- Once the cover is gone, you will see the filter. It is usually made of sponge, foam or a similar material.
- If you want to replace the filter, remove the filter and put in a new one. Put the cover back on.
- If you want to clean it, put the filter in a container of soapy water. Squeeze the filter to remove the dirt, but take care not to tear it up. Rinse the filter well.
- Put the filter back on the blower. Place the cover on. You can try the blower again to see if it works.
Cleaning the air filter regularly definitely helps. But if the filter is always getting dirty or the engine gets hot quickly, it might be time to buy a replacement.
Damaged Recoil Pulley
Most blowers use a starter cord. You pull and let go of the cord and a spring recoils the cord. If the recoil is damaged, the cord cannot recoil. If this happens, the engine will not start.
Solution. Replace the recoil spring. It might be possible to fix the rope and spring, but in these cases it is faster to just buy a replacement spring. You can find one that matches your leaf blower model by checking the official manufacturer site.
Add Seafoam to the Fuel
Fuel varnish can cause problems with the carburetor, making it difficult to start a leaf blower, but Seafoam can help. It is a popular product used to lubricate engines. It can remove oil sludge, varnish and other deposits in the engine.
Solution. Use the following steps to apply Seafoam to your leaf blower engine. Pour a quarter of Seafoam in a 2-stroke engine. For a 4-stroke, pour three quarters. Check the product instructions if it recommends a different amount. Follow the indications there.
Turn the engine on. Let it idle for 6 minutes then shut it off. Do not turn the engine on for two straight days. Do not remove the fuel with Seafoam in it.
After two days, turn on the leaf blower. By this time Seafoam should have removed all the varnish in the engine. This also works with other outdoor tools and is better than using starter fluid.
Compression is Too Low
Leaf blowers must have a compression rating of 90-150 PSI. The bigger the engine, the higher the compression has to be.
Solution. Use a compression tester to check the compression level of your leaf blower. Follow these steps.
- Take off the cylinder cover.
- You will see the spark plug boot. Give it a soft pull to detach from the spark plug. Use a screwdriver to completely remove the boot.
- Use a wrench to remove the spark plug.
- Put the compression tester fitting end into the spark plug opening. Rotate it clockwise.
- Once the tester is secure, pull the starter rope 3-5 times. At this point, the tester will indicate the compression level.
If the compression is below 90, you have to increase it. Here is how you do it.
Check if the spark plug and/or the threading are loose. If you can turn them by hand, then it is loose. You have to replace either the plug, threading or both.
Tighten the bolts on the engine. Even if just a few of these come loose, it can reduce compression and prevent the blower from running.
Blown gasket. Gaskets are essential to keep compression at the right level. If the gasket gets damaged, the compression will drop. A leaking gasket will prevent leaf blowers from working right when it is hot. The solution is to replace the gasket.
Broken cylinder head. The cylinder head generates the compression in leaf blowers. Replace the cylinder if there is any crack.
Vapor lock. Vapor lock occurs when fuel evaporates due to heat. The fuel mixture becomes too lean so the blower cannot function.
This usually affects old leaf blowers. Vapor lock can also occur at high temperature, high engine temperature, damaged fuel lines and using old fuel. Turn the blower off and move it someplace cool or under shade. Open the fuel tank to further cool it. After a few minutes, turn the blower on.
Broken Carburetor Diaphragm
Blower carburetors have several diaphragms which replenishes, measures and mixes the fuel. When the fuel is ready the diaphragm transmits it to the cylinder. These diaphragms get worn out with constant use and this can prevent a leaf blower from starting up.
Solution. It takes a long time and a lot of use to wear diaphragms out, so it may just need cleaning. Clan the carburetor and while you are at it, check the diaphragm and other parts. If the diaphragm looks fine, the carburetor just needs maintenance.
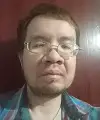
I love the outdoors and all the tools for maintaining gardens, yards and lawns. The only thing I am more passionate about is sharing what I know about garden and outdoor equipment.